In an era where medical science continues to revolutionize our world, the challenge of maintaining cold chain integrity has never been more critical. The temperature-controlled logistics and pharmaceutical sectors are under constant pressure to preserve the quality of life-saving drugs and vaccines from manufacturing facilities to the patients who need them.
Ensuring Cold Chain Integrity during the packaging and transportation process is a formidable task, with global implications for public health and safety. Dive into this post to understand the intricacies involved in maintaining temperature control, and explore how cutting-edge technologies are helping overcome these challenges. This is not just about logistics or pharmaceuticals; it’s about safeguarding lives, one degree at a time.
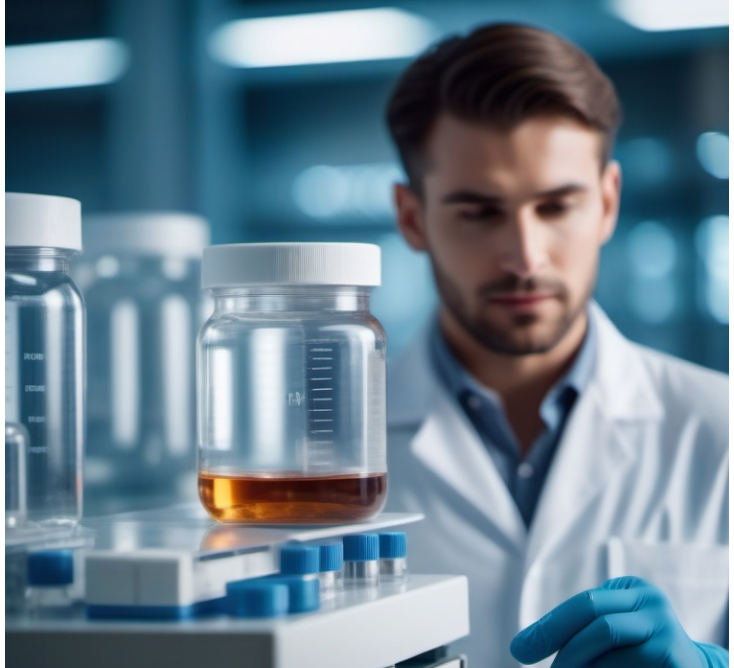
What is Cold Chain Integrity?
Cold chain integrity refers to the maintenance and preservation of the desired temperature throughout the supply chain for temperature-sensitive products, such as food, pharmaceuticals, and chemicals. It involves proper packaging, temperature control, and monitoring to ensure that these products remain within their required temperature range from production to consumption.
Deviations from the required temperature can result in spoilage, reduced shelf life, or compromised quality and efficacy. Our article provides a comprehensive understanding of the importance of cold chain integrity and offers insights on how to identify and prevent breaches in the cold chain.
Cold Chain in Logistics and Pharmaceuticals
In both the logistics and pharmaceutical industries, maintaining the integrity of the cold chain is of utmost importance. The cold chain refers to the temperature-controlled supply chain that ensures the safe packaging, transportation, storage, and handling of temperature-sensitive products, such as vaccines, medications, and other healthcare products. It plays a critical role in preserving product efficacy and safety from the point of manufacture to the end-user.
Let’s consider a scenario where vaccines are being transported across continents. Without proper temperature control throughout the journey, including during transportation, customs clearance, and storage at various points, there is a high risk of compromising the vaccines’ potency, rendering them useless or even harmful. Ensuring the integrity of the cold chain becomes paramount in such situations.
The cold chain involves a complex network of stakeholders, including manufacturers, distributors, transporters, and storage facilities. Each entity has a specific role to play in maintaining temperature control and preventing breaches that could impact product quality. Key components of the cold chain include:
- Temperature Monitoring: Accurate and continuous monitoring of temperature is essential to identify any deviations from specified ranges. This involves using sophisticated sensors and data loggers that provide real-time data on temperature conditions.
- Packaging and Insulation: Specialized packaging materials with insulation properties create a barrier against external temperature fluctuations. These materials help maintain consistent temperatures during transportation.
- Transportation: Temperature-controlled vehicles or containers equipped with refrigeration units are used to transport temperature-sensitive products safely. Different modes of transport, such as air freight or road transportation, may be employed based on the urgency and distance of shipment.
- Storage Facilities: Properly designed warehouses or cold storages ensure controlled temperature environments for appropriate product storage. Temperature-controlled areas are divided into zones based on specific requirements for different products.
- Standard Operating Procedures (SOPs): Implementing robust SOPs helps ensure that all stakeholders involved in the cold chain adhere to standardized protocols. This includes guidelines for handling, storage, transportation, and temperature monitoring.
Key Components and Role
The successful implementation of the cold chain relies on various stakeholders working collaboratively to maintain temperature control and product integrity. Let’s consider some of the key players and their roles:
- Manufacturers: Pharmaceutical manufacturers play a crucial role in ensuring that their products are manufactured, packaged, and labeled appropriately for temperature-sensitive distribution. They must adhere to regulatory standards and good manufacturing practices (GMP) to guarantee product quality.
- Logistics Service Providers: Logistics companies specializing in healthcare or pharmaceutical logistics provide expertise in transporting temperature-sensitive products. They offer specialized vehicles, containers, and facilities equipped with refrigeration systems to maintain optimal temperatures during transit.
- Third-Party Logistics (3PL) Providers: 3PL providers often handle storage and distribution operations on behalf of manufacturers or distributors. They manage inventory, order fulfillment, and shipping while ensuring adherence to cold chain requirements.
- Regulatory Authorities: Regulatory bodies enforce strict guidelines for the storage, handling, transportation, and packaging of temperature-sensitive products. They establish standards that manufacturers, distributors, and other stakeholders must comply with to maintain product quality and patient safety.
- Healthcare Providers: Hospitals, clinics, pharmacies, and other healthcare institutions receive temperature-sensitive products for administration or dispensing to patients. They must have appropriate storage conditions in place to ensure product efficacy when administered.
Each stakeholder within the cold chain has a shared responsibility to uphold temperature control measures. By actively participating and fulfilling their respective roles, they collectively contribute to preserving the integrity of the cold chain.
Risk Factors for Breaches
Maintaining cold chain integrity is a complex task, and there are numerous factors that can lead to breaches in temperature control. These breaches can occur at various stages of the supply chain, from transportation to loading, unloading, and warehousing. Understanding these risk factors is crucial in order to implement effective preventative measures.
One significant risk factor is the malfunctioning of equipment or power interruptions during transportation. Even with the use of refrigerated trailers or containers (reefer services), which are common in temperature-controlled transport and storage, there is still a potential for equipment failure that could compromise the integrity of the cold chain. These malfunctions can disrupt proper temperature maintenance and result in the degradation or spoilage of products.
Another risk factor is inadequate air circulation within warehouses or storage facilities. Proper airflow is essential for distributing and maintaining the desired temperature throughout the space. Defective insulation can also contribute to breaches in cold chain integrity by allowing external temperatures to affect the products stored inside. Extended periods spent on loading docks without proper temperature control can further exacerbate these issues.
Improper handling during transshipment can also pose risks to cold chain integrity. For instance, turning off refrigeration units during transshipment or failing to monitor temperature maintenance can cause products to be exposed to unfavorable conditions, leading to compromised quality or even spoilage.
It’s important to identify these potential risk factors and take appropriate actions to mitigate them. Continuous monitoring and regular inspections along the supply chain can help pinpoint locations where breaches in cold chain integrity may occur. By being vigilant, companies can promptly address issues that might compromise product quality and shelf life.
Importance of Compliance Standards in Cold Chain Integrity
Compliance with industry standards and regulations is of utmost importance when it comes to maintaining cold chain integrity. With specific guidelines in place, businesses can ensure that every stage of their operations adheres to strict requirements, mitigating the risks associated with breaches in temperature control.
Let’s consider the pharmaceutical industry, where compliance standards are essential for preserving the efficacy and safety of drugs. Certain medications require strict temperature control in order to remain effective. Breaches in cold chain integrity can result in the degradation of these drugs, rendering them ineffective or potentially harmful. Compliance with temperature control regulations ensures that medications can be safely transported and stored without compromising their quality.
Similarly, compliance standards play a crucial role in ensuring food safety and traceability. For instance, organizations involved in the cold chain for perishable goods must adhere to regulations that govern the handling, transportation, and packaging of food products. The failure to comply with these standards can lead to foodborne illnesses or contamination, jeopardizing consumer health and brand reputation.
Moreover, compliance standards help improve overall supply chain visibility and transparency. Organizations that comply with regulations can provide accurate documentation and track the movement of products at every stage. This ability enhances traceability and accountability, allowing for quick identification of breaches in cold chain integrity should they occur.
By upholding compliance standards, businesses demonstrate their commitment to quality assurance and customer satisfaction. They are better equipped to prevent breaches in cold chain integrity and maintain the trust of their partners, customers, and regulators.
Food Safety and Traceability
In the world of cold chain logistics, ensuring food safety and traceability is of paramount importance. Foodborne illnesses can have severe consequences for individuals’ health, and the ability to trace the origin and movement of food products is crucial in identifying and mitigating risks.
When it comes to preserving food quality and safety throughout the cold chain, several factors come into play. The process starts at the production stage, where rigorous food safety measures are implemented to prevent contamination. This includes maintaining hygienic practices during cultivation, harvesting, and processing to minimize the risk of bacterial growth or cross-contamination. Additionally, proper storage conditions and temperature control play a vital role in preventing spoilage and maintaining product integrity.
Let’s consider an example of fresh produce being transported from a farm to a supermarket. As soon as the produce is harvested, it must be rapidly cooled to the appropriate temperature to slow down enzymatic reactions and maintain freshness. Proper packaging is also critical to protect the produce from physical damage during transportation. Throughout the supply chain, temperature monitoring devices are used to ensure that the recommended temperature range is maintained consistently.
Traceability is equally important in ensuring food safety within the cold chain. Through advanced technologies like barcode systems or radio frequency identification (RFID) tags, each food product can be tracked and traced from its origin to its final destination. This enables rapid identification in case of a recall or outbreak of foodborne illness, facilitating prompt action to safeguard public health.
Some critics argue that implementing comprehensive traceability systems across the entire cold chain can be costly for businesses. However, it is essential to consider the potential long-term benefits such as improved consumer confidence in food safety. A single instance of a significant recall due to contaminated or unsafe products can severely damage a company’s reputation and result in financial losses far greater than the investment required for traceability initiatives.
Strategies for Cold Chain Integrity
Maintaining cold chain integrity is essential to preserve the efficacy and safety of pharmaceutical products. Let’s delve into some key strategies that can be employed to uphold temperature control throughout the supply chain.
- Robust Temperature Monitoring: Deploying reliable temperature monitoring techniques, such as data loggers or real-time tracking systems, allows continuous monitoring of product temperatures at various stages. This helps identify any temperature excursions promptly and ensures prompt action can be taken to prevent product spoilage or compromise.
- Efficient Packaging Solutions: Employing appropriate packaging solutions tailored to the specific requirements of the pharmaceuticals being transported is crucial. Insulated containers and gel packs, and passive cooling technologies are commonly used to maintain temperature stability during transportation.
- Streamlined Documentation and Record-Keeping: Detailed documentation is necessary to track the movement of pharmaceutical products along the cold chain. This includes information about product storage conditions, handling procedures, and any deviations encountered during transportation. Establishing a robust record-keeping system enhances transparency and enables efficient management of potential temperature excursions.
- Staff Training and Education: Ensuring all personnel involved in cold chain management receive comprehensive training on best practices is vital. This includes understanding temperature-sensitive products’ handling requirements, proper use of monitoring equipment, and adherence to standard operating procedures (SOPs).
- Collaboration and Communication: Effective communication and collaboration among stakeholders within the cold chain network are paramount. This includes clear channels for sharing information about product specifications, storage requirements, potential risks, and emerging challenges. Regular meetings or forums can facilitate knowledge sharing and foster collaboration.
For instance, a pharmaceutical manufacturer could collaborate with logistics partners to develop shared protocols for temperature control. This could involve joint training sessions, exchange of best practices, and regular communication to ensure alignment and compliance with cold chain requirements.
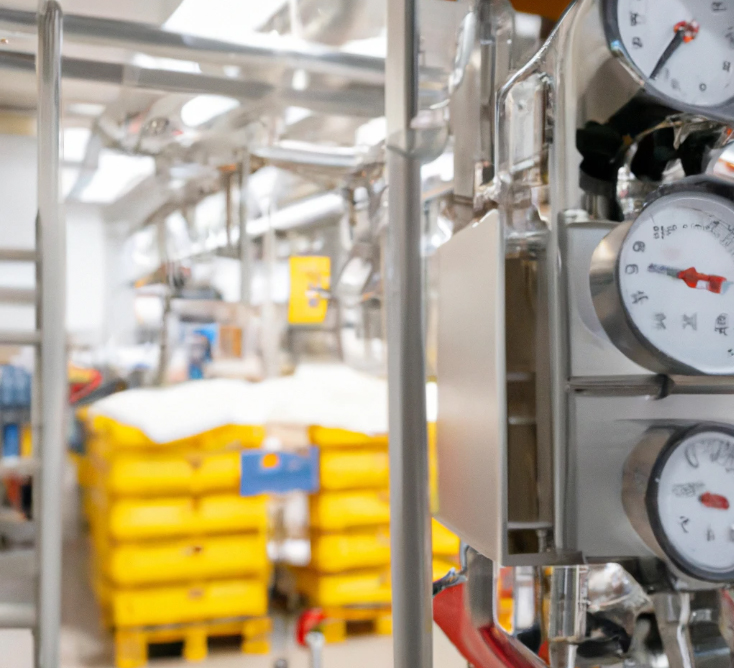
Implementing these strategies can significantly contribute to maintaining cold chain integrity and ensuring the safe packaging and delivery of pharmaceutical products. However, challenges may arise during the process, such as managing temperature excursions and transportation to remote locations with limited infrastructure. It is essential to address these challenges collectively and continuously evaluate and improve systems for optimal cold chain management.
- Maintaining cold chain integrity is crucial for preserving the efficacy and safety of pharmaceutical products. To uphold temperature control throughout the supply chain, key strategies include robust temperature monitoring, efficient packaging solutions, streamlined documentation and record-keeping, staff training and education, and collaboration and communication among stakeholders. Implementing these strategies can help prevent product spoilage or compromise. Challenges may arise, such as managing temperature excursions and transportation to remote locations, but addressing them collectively and continuously improving systems is essential for optimal cold chain management.
Temperature Monitoring Techniques and Innovations
Ensuring temperature control in logistics and pharmaceuticals is vital to maintain the integrity of products that are sensitive to temperature fluctuations. To achieve this, various temperature monitoring techniques and innovations have emerged to provide accurate and real-time data. These advancements enable businesses to address potential issues promptly and take proactive measures to prevent product spoilage or compromised quality.
One such technique is the use of temperature data loggers. These devices are equipped with sensors that continuously monitor and record temperature levels during transportation and storage. They provide valuable information about temperature excursions, allowing stakeholders to identify where and when deviations occurred. Integrated with software systems or cloud platforms, data loggers offer convenience by automatically generating detailed reports and alerts for immediate action.
Consider a scenario where a pharmaceutical company needs to ship vaccines that require strict temperature control. By using temperature data loggers, they can track the temperature conditions throughout the entire journey, from manufacturing facilities to distribution centers. If any deviations above or below the specified range occur, an alert is triggered, allowing the company to intervene promptly.
Advanced technologies like IoT (Internet of Things) have also paved the way for enhanced temperature monitoring capabilities. IoT-enabled devices can transmit real-time temperature data wirelessly, eliminating manual checks and reducing human error. This connectivity enables seamless integration with other supply chain systems, facilitating automated actions such as adjusting cooling settings or rerouting shipments in case of emergencies.
Additionally, innovative solutions like smart labels and RFID (Radio Frequency Identification) tags have revolutionized temperature monitoring within the cold chain. These compact devices can be attached directly to product packaging or containers, providing continuous tracking without obstructing normal operations. With RFID technology, relevant stakeholders can access critical information by simply scanning tags with handheld devices or using fixed readers at various checkpoints along the supply chain.
As technology continues to evolve and play a crucial role in maintaining cold chain integrity, it’s essential to recognize the real-world challenges that often hinder effective temperature control.
Real-world Challenges in Maintaining Cold Chain Integrity
Despite the advancement of temperature monitoring techniques and innovations, several real-world challenges persist in maintaining cold chain integrity. These challenges arise across various stages of the supply chain and require proactive strategies to overcome them.
One significant challenge is the capital investment required to establish and maintain an efficient cold chain infrastructure. Building or upgrading warehouses, installing refrigeration units, and implementing temperature monitoring systems can incur substantial costs. Small businesses or those operating in resource-limited regions may struggle to make these investments, potentially compromising the quality and safety of temperature-sensitive products.
Consider a local farmer who wants to expand their business by exporting fresh produce overseas. While they have high-quality products, they lack the financial means to invest in refrigerated storage facilities and temperature monitoring technology. As a result, their products may experience quality deterioration during transportation, leading to customer dissatisfaction and financial losses.
Energy consumption is another challenge tied to maintaining a robust cold chain. Refrigeration units and temperature-controlled vehicles consume significant energy, contributing to carbon emissions and environmental impact. Finding sustainable solutions that minimize energy consumption without compromising temperature control effectiveness is crucial for long-term viability.
Think of it as finding a delicate balance between preserving product quality and minimizing environmental harm, much like walking on a tightrope – one misstep can have detrimental consequences.
Limited resources, such as reliable power supply or adequate storage space in certain regions, pose additional obstacles to maintaining cold chain integrity. Developing countries or remote areas may face infrastructural limitations that make it challenging to achieve consistent temperature control throughout the supply chain. This highlights the need for tailored solutions that consider specific regional demands and constraints.
While technology plays a vital role in addressing some of these challenges, collaboration among stakeholders across the cold chain is equally essential. By pooling resources, knowledge, and expertise, businesses, logistics providers, regulators, and other relevant parties can collectively strive towards a resilient cold chain system that ensures temperature control integrity.